Key Takeaways:
- Ultrasonic welding is a cutting-edge technology that joins thermoplastic materials through high-frequency vibrations and frictional heat.
- The process parameters, joint design, and material compatibility are crucial factors influencing the success of ultrasonic welding.
- Ultrasonic welding finds applications in various industries, providing unmatched speed, safety, and joint reliability.
- While ultrasonic welding offers numerous advantages, it has limitations in terms of material compatibility, joint complexity, and initial investment.
Introduction: Solving the Puzzle of Ultrasonic Welding
Have you ever wondered how two materials can be seamlessly joined together without the need for adhesives or fasteners? The answer lies in the innovative technology of ultrasonic welding. In this article, we will delve into the depths of this intriguing process and understand how it has revolutionized various industries.
Are you ready to unlock the secrets of ultrasonic welding and discover its vast potential? If so, let’s embark on this enlightening journey together!
Definition of Ultrasonic Welding
Ultrasonic welding is a sophisticated manufacturing technique used to join thermoplastic materials together by converting high-frequency mechanical vibrations into frictional heat. This heat leads to the formation of a strong molecular bond between the materials, creating a secure and robust joint.
Principle of Operation
High-Frequency Vibrations
At the heart of ultrasonic welding lies the generation of high-frequency vibrations, typically in the range of 20 kHz to 70 kHz. These vibrations are produced by an ultrasonic generator and are transmitted to the materials to be welded.
Generating Frictional Heat
When the high-frequency vibrations encounter the joint interface between the materials, they create intense friction. This friction generates heat, causing the thermoplastic materials to soften at their contact points.
Formation of a Molecular Bond
As the materials reach their melting point due to the generated heat, the frictional forces press them together. The softened plastic materials merge and form a molecular bond as they cool and solidify.
Thermoplastic Materials and Joint Design Considerations
To ensure successful ultrasonic welding, the choice of thermoplastic materials is critical. Materials like polyethylene, polypropylene, ABS, and polycarbonate are commonly used due to their favorable characteristics for the process.
Moreover, the joint design plays a pivotal role in the welding process. Factors such as the joint geometry, surface finish, and precision alignment greatly influence the welding outcome.
Utilizing Dissimilar Materials in the Process
Ultrasonic welding has the remarkable ability to join dissimilar materials effectively. This characteristic expands its applications and allows manufacturers to create innovative products by combining materials with diverse properties.
Process Parameters
The ultrasonic welding process involves several key parameters that influence the quality and reliability of the joint. Understanding and optimizing these parameters are essential for successful welding outcomes:
1. Weld Time
The duration of the ultrasonic vibrations applied to the joint is known as the weld time. Proper adjustment of the weld time ensures optimal bonding and prevents under or over-welding.
2. Weld Cycle
The complete sequence of welding actions, including the application of ultrasonic vibrations, holding time, and retraction of the horn, constitutes the weld cycle.
3. Electrical Energy Input
The amount of electrical energy supplied to the ultrasonic welding system affects the amplitude of vibrations and, consequently, the heat generation.
4. Filler Material
In some cases, adding a compatible filler material to the joint can improve the weld strength and integrity.
5. Horn Contact
The horn, which transmits vibrations to the joint, must make proper and consistent contact to ensure uniform heat distribution.
6. Pressure Applied
Applying the right amount of pressure during the welding process is crucial for achieving a strong and durable bond.
7. Hold Time
The hold time refers to the duration for which pressure is maintained after the ultrasonic vibrations stop. It allows the materials to solidify and the bond to stabilize.
8. Horn Retracts
After the hold time, the ultrasonic horn retracts, and the welded parts can be removed.
Comparison of Ultrasonic Welding with Traditional Methods
Ultrasonic welding boasts several advantages over conventional joining methods, particularly Mechanical Fastening, Adhesive Bonding, and Hot Plate Welding. Let’s examine the key differences:
Aspect | Ultrasonic Welding | Mechanical Fastening | Adhesive Bonding | Hot Plate Welding |
---|---|---|---|---|
Joining Speed | Remarkably Fast | Moderate | Moderate | Moderate |
Joining Strength | Excellent | Strong | Strong | Strong |
Additional Materials Required | No | Yes | Yes | Yes |
Post-Weld Processing | Minimal | Some | Some | Some |
Aesthetic Finish | Yes | Varies | Yes | Yes |
Stress Distribution | Even and Uniform | Varies | Varies | Even and Uniform |
Environmental Impact | Low (No Emissions) | Moderate | Varies | Moderate |
Main Parts of Ultrasonic Welding Machine
To understand the functioning of ultrasonic welding, it’s essential to familiarize ourselves with the key components of the ultrasonic welding machine:
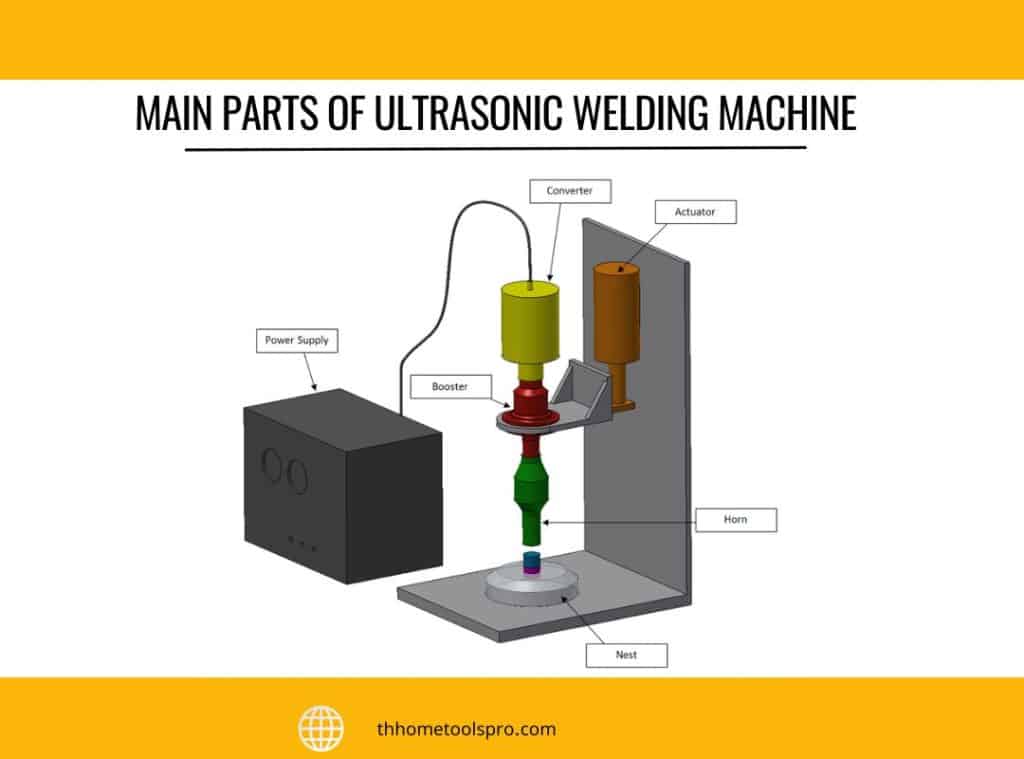
Generator
The ultrasonic generator is responsible for producing the high-frequency electrical energy required for generating vibrations.
Machine Press
The machine press holds and positions the materials to be welded securely during the process.
Welding Stack
The welding stack consists of the transducer, booster, and welding horn, amplifying and transmitting vibrations to the joint.
Transducer
The transducer converts the high-frequency electrical energy from the generator into mechanical vibrations.
Booster
The booster serves to amplify and optimize the vibrations transmitted to the welding horn.
Welding Horn
The welding horn, also known as the sonotrode, directly contacts the joint and transmits the ultrasonic vibrations to the materials.
Support Tooling
Support tooling ensures accurate alignment and positioning of the materials for consistent and reliable welding.
Applications of Ultrasonic Welding
Ultrasonic welding has become an indispensable technology across various industries, enabling manufacturers to create sturdy and precise assemblies. Some prominent applications include:
1. Computing and Electrical
In the electronics industry, ultrasonic welding is commonly used to assemble delicate components, ensuring a secure and reliable connection.
2. Aerospace and Automotive
Ultrasonic welding finds extensive use in the aerospace and automotive sectors, facilitating the assembly of lightweight components and ensuring airtight seals.
3. Medical
The medical industry relies on ultrasonic welding to create leak-proof and hygienic joints for medical devices and equipment.
4. Packaging
Ultrasonic welding is instrumental in manufacturing leak-resistant and tamper-evident seals for various packaging materials.
5. Textiles
The textile industry utilizes ultrasonic welding to join fabrics without the need for additional stitching or adhesives.
6. Appliances
In the manufacturing of household appliances, ultrasonic welding enables precise and robust connections, enhancing product durability.
Important Factors of Ultrasonic Plastic Welding
While ultrasonic welding offers numerous advantages, certain critical factors must be considered for successful plastic welding:
1. Material Compatibility
Ensuring that the thermoplastic materials to be welded are compatible with ultrasonic welding is crucial for obtaining strong and reliable joints.
2. Energy Director Design
An energy director design in the joint area enhances the efficiency of ultrasonic energy transfer, promoting better bonding.
3. Cleanliness of Components
Contaminants or foreign particles on the joint surfaces can adversely affect the welding process, necessitating meticulous cleaning.
4. Amplitude Control
Proper control of the ultrasonic vibrations’ amplitude ensures optimal energy delivery, preventing material damage.
5. Weld Depth Control
Controlling the depth of the weld prevents excessive penetration or insufficient bonding.
The Advantages of Ultrasonic Welding
Ultrasonic welding brings forth a myriad of benefits that have made it a preferred choice for joining thermoplastic materials:
1. The Speed
Ultrasonic welding is an incredibly fast process, completing joints within seconds, leading to enhanced productivity and reduced manufacturing time.
2. Unmatched Safety
Unlike some traditional methods that may require heat, flames, or adhesives, ultrasonic welding is a safe and eco-friendly process with no toxic emissions.
3. Reliability
The molecular bonds formed in ultrasonic welding result in strong and consistent joints that withstand rigorous conditions.
4. Flexibility
The ability to join dissimilar materials expands the range of applications for ultrasonic welding, making it versatile and adaptable.
5. Minimal Material Costs
As ultrasonic welding does not require additional fasteners or adhesives, material costs are significantly reduced.
6. Joint Quality
Ultrasonic welding produces aesthetically pleasing and hermetically sealed joints, enhancing the overall quality of the final product.
The Disadvantages of Ultrasonic Welding
While ultrasonic welding offers many advantages, it also has some limitations that must be considered:
1. Limits Material
Ultrasonic welding is suitable for thermoplastic materials only, restricting its use to certain applications.
2. Limits the Sizes
The size of the materials that can be welded is limited by the capacity of the ultrasonic welding machine.
3. A High Initial Investment
Setting up an ultrasonic welding system requires a considerable initial investment, which may be a deterrent for some businesses.
4. Limits the Joint Types
Certain complex joint designs may not be feasible with ultrasonic welding.
5. Lead Time
For intricate assemblies, ultrasonic welding may require additional preparation and setup time.
Conclusion: Embracing the Power of Ultrasonic Welding
In conclusion, ultrasonic welding stands as a remarkable technological achievement in the world of manufacturing and fabrication. Its ability to join thermoplastic materials swiftly, securely, and cost-effectively has made it an invaluable asset across numerous industries.
From computing and aerospace to medical and packaging, the applications of ultrasonic welding continue to grow, opening up new possibilities for creative and efficient product designs.
As you dive deeper into the realm of ultrasonic welding, you will uncover its true potential and discover innovative ways to enhance your manufacturing processes. Let this knowledge empower you to explore the boundless horizons of ultrasonic welding and unlock the future of precision assembly!
Frequently Asked Questions (FAQs)
1. What materials can be joined using ultrasonic welding? Ultrasonic welding is primarily used for joining thermoplastic materials such as polyethylene, polypropylene, ABS, and polycarbonate.
2. How does ultrasonic welding compare to traditional welding methods? Unlike traditional methods, ultrasonic welding offers faster joining speeds, unmatched safety, higher reliability, minimal material costs, and aesthetically pleasing joint quality.
3. Can ultrasonic welding be used for dissimilar materials? Yes, one of the significant advantages of ultrasonic welding is its ability to join dissimilar materials effectively, allowing for innovative product designs.
4. What are the main components of an ultrasonic welding machine? The key components of an ultrasonic welding machine include the generator, machine press, welding stack (consisting of the transducer, booster, and welding horn), and support tooling.
5. What are the primary applications of ultrasonic welding? Ultrasonic welding finds applications in computing and electrical industries, aerospace and automotive sectors, medical devices, packaging, textiles, and household appliances.
6. What are the limitations of ultrasonic welding? Ultrasonic welding is limited to thermoplastic materials, has size restrictions, requires a high initial investment, and may not be suitable for complex joint designs.
Data Sources: