Key Notes
Here are some key notes and takeaways about types of welding:
- Welding is a process that involves joining two or more pieces of metal together by heating them to a molten state and allowing them to cool and solidify.
- There are many different types of welding, each with its own advantages, limitations, and applications.
- Some of the most common types of welding include fusion welding, solid-state welding, arc welding, resistance welding, and oxyfuel gas welding.
- Each type of welding requires specialized equipment, materials, and techniques, and may be suitable for different types of metals, thicknesses, and applications.
- Some of the factors to consider when choosing a welding process include the required strength, durability, precision, and cost-effectiveness of the weld, as well as the type of metal, thickness, and shape of the materials being welded.
- Welding is a complex and technical process that requires proper training, equipment, and safety precautions to ensure that the weld is strong, durable, and safe to use.
- Welding can be used in a wide range of industries and applications, including construction, manufacturing, automotive, aerospace, and electronics, and can be used to create everything from custom metalwork to structural components and machinery.
Overall, understanding the different types of welding and their applications is essential for selecting the right welding process for a specific job, as well as ensuring that the weld is strong, durable, and safe to use. Proper training, equipment, and safety precautions are also crucial for achieving successful and reliable welds.
Take Away
Welding is a process used for connecting or joining two pieces of metal together by the use of heat, pressure, and sometimes other materials. It is one of the most common methods of fabrication in industrial settings. Welding is used to create a permanent connection between two metals, and can be used to join different types of metals such as aluminum, steel, brass, copper, and titanium.
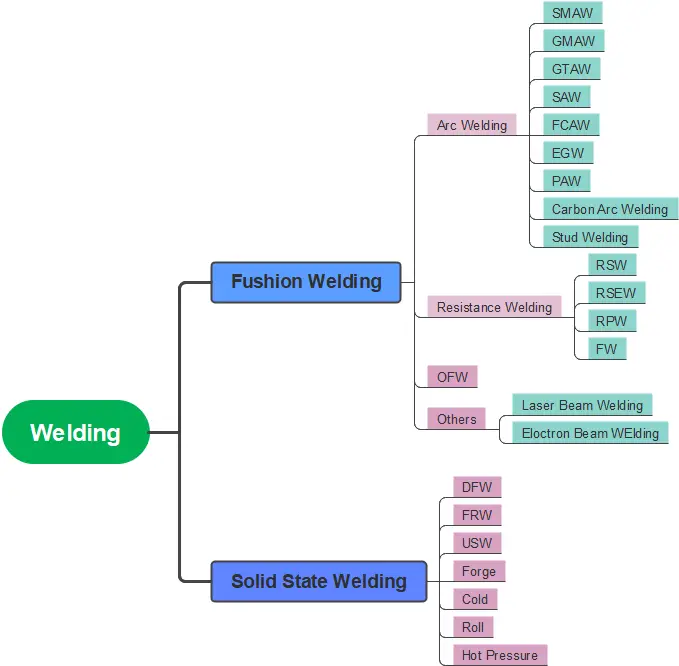
Fusion Welding
Fusion welding is a type of welding process that involves melting and fusing two or more metal parts together. It is one of the most common types of welding used in various industries, such as construction, automotive, and aerospace.
In fusion welding, the metal parts to be joined are heated to their melting point using various heat sources, such as an electric arc or a gas flame. Once the metal parts have melted, they are fused together to form a strong and permanent joint.
Some of the common types of fusion welding include:
- Gas Tungsten Arc Welding (GTAW): Also known as Tungsten Inert Gas (TIG) welding, GTAW uses a tungsten electrode to create an electric arc between the metal parts and a shielding gas to protect the weld from atmospheric contamination.
- Gas Metal Arc Welding (GMAW): Also known as Metal Inert Gas (MIG) welding, GMAW uses a wire electrode that is continuously fed through a welding gun and a shielding gas to protect the weld from atmospheric contamination.
- Submerged Arc Welding (SAW): SAW involves using a granular flux to cover the weld and a continuous wire electrode to feed the weld pool. The weld is made beneath the flux, which protects it from atmospheric contamination.
- Plasma Arc Welding (PAW): PAW uses a concentrated plasma arc to melt the metal parts and form the weld. To safeguard the weld from contamination by atmospheric gases, a shielding gas is employed.
Fusion welding is known for producing high-strength and high-quality welds. It is commonly used to join metal parts that require a high level of structural integrity, such as in construction, automotive, and aerospace applications.
Arc Welding
Arc welding is a type of welding process that uses an electric arc between an electrode and the metal workpiece to create a weld. The electric arc melts the metal workpiece and the electrode, and the molten metal fuses to form a weld. Arc welding is one of the most common types of welding used in various industries, such as construction, shipbuilding, and automotive.
Arc welding is known for its versatility and ability to weld a wide range of metals, including steel, aluminum, and copper. It is commonly used in industries that require strong and reliable welds, such as construction, shipbuilding, and automotive.
There are several types of arc welding, including:
1. Shielded Metal Arc Welding (SMAW)
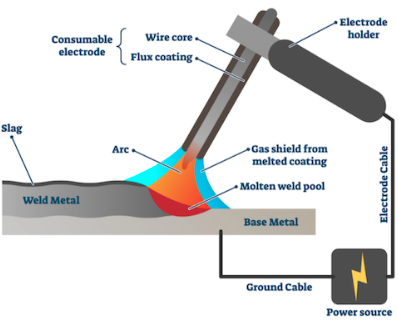
Also known as Stick welding, SMAW is a type of arc welding that uses a consumable electrode coated in flux to create the electric arc. The flux coating melts and forms a protective gas shield around the weld, protecting it from atmospheric contamination.
2. Gas Tungsten Arc Welding (GTAW)

Gas Metal Arc Welding (GMAW), also known as Metal Inert Gas (MIG) welding, is a welding process that utilizes a wire electrode, which is continuously fed through a welding gun, and a shielding gas, which is directed over the weld pool to prevent contamination by atmospheric gases. According to data from the American Welding Society, GMAW is one of the most widely used welding processes in industrial applications, accounting for approximately 60% of total welding activities in the United States.
3. Gas Metal Arc Welding (GMAW)

GMAW, which is also referred to as Metal Inert Gas (MIG) welding, involves feeding a wire electrode continuously through a welding gun and directing a shielding gas over the weld pool to prevent contamination by atmospheric gases
4. Flux-Cored Arc Welding (FCAW)
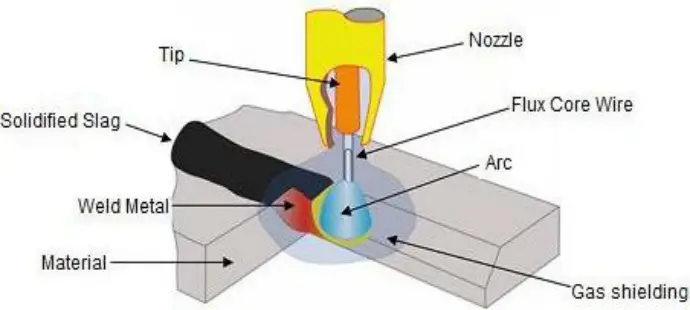
FCAW uses a tubular wire electrode that is filled with flux to create the electric arc. The flux generates a shielding gas, protecting the weld from atmospheric contamination.
5. Submerged Arc Welding (SAW)
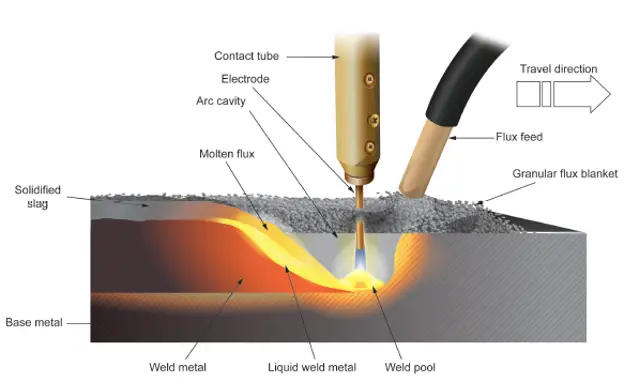
Stands for Submerged Arc Welding, which is a type of welding process that involves the formation of a weld between two metal parts by generating an electric arc between a consumable electrode and the workpiece. The arc is submerged beneath a granular flux, which prevents atmospheric contamination and provides insulation to the arc.
6. Electrogas Welding (EGW)
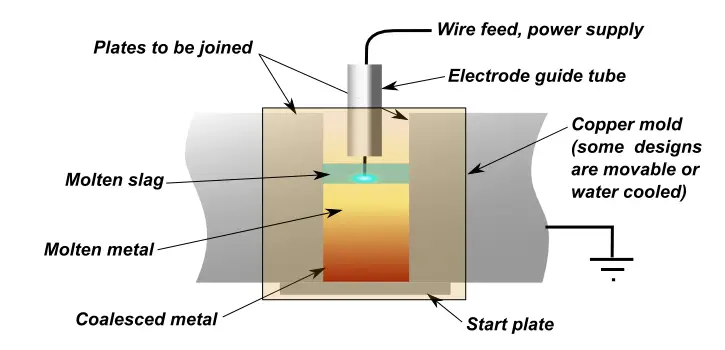
Which is a type of welding process that uses a consumable electrode and a continuous supply of flux to create a weld between two metal parts. It is a variation of the Gas Metal Arc Welding (GMAW) process, also known as MIG welding.
In Electrogas Welding, a consumable electrode is fed continuously into the weld joint, and the weld pool is shielded by a flux that is delivered through a nozzle. The weld is formed by the heat generated from an electric arc between the electrode and the workpiece.
EGW is often used for welding thick sections of steel plate in shipbuilding, offshore, and other heavy fabrication industries. It is suitable for both flat and curved surfaces and can be used in both vertical and horizontal welding positions.
7. Plasma Arc Welding (PAW)
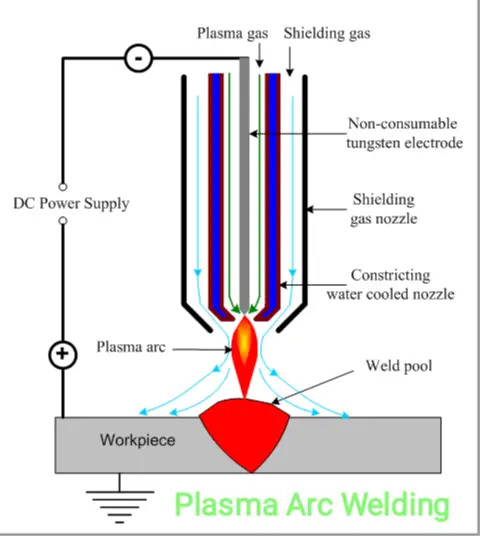
PAW stands for Plasma Arc Welding, which is a type of welding process that uses a focused plasma arc to create a weld between two metal parts. Plasma is a high-temperature ionized gas that is created by passing an electric current through a gas, such as argon or helium.
In plasma arc welding, a tungsten electrode is used to generate the plasma arc, which is then focused onto the metal parts using a nozzle. As the plasma arc makes contact with the metal parts, it generates intense heat, which melts the metal and fuses the parts together.
Plasma arc welding is commonly used in the aerospace, automotive, and manufacturing industries, where high-precision welds are required.
8. Carbon Arc Welding (CAW)
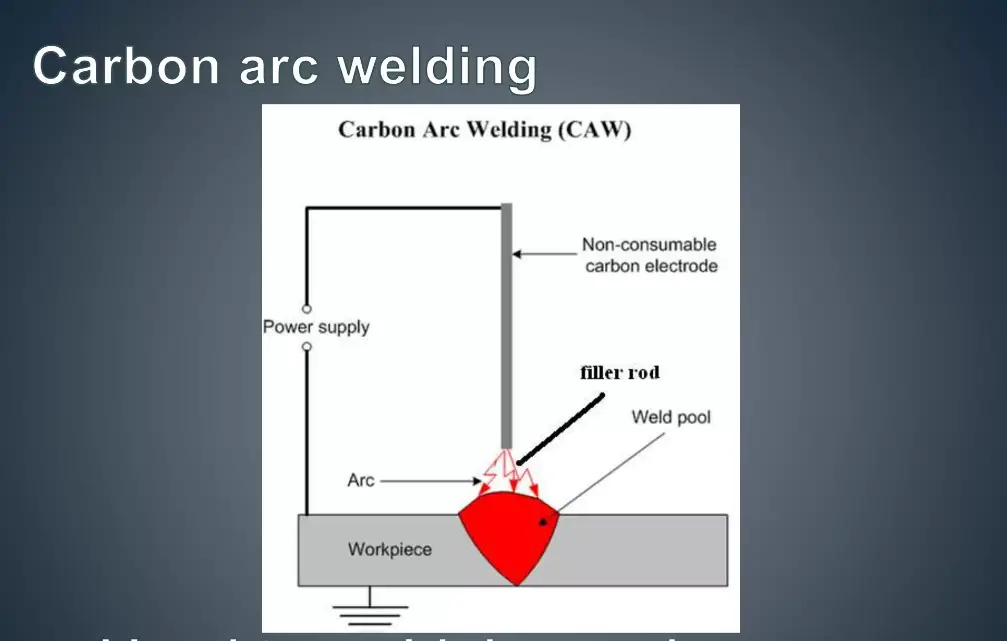
Carbon Arc Welding (CAW) is a welding process that uses a carbon electrode to create an electric arc between the electrode and the workpiece, generating heat that melts the metal and fuses the parts together. The carbon electrode is held in a holder and connected to a power source that produces an electric current.
Unlike other arc welding processes such as Shielded Metal Arc Welding (SMAW) or Gas Tungsten Arc Welding (GTAW), the carbon electrode used in CAW is not consumed during the welding process. Instead, the heat generated by the arc melts the metal, and the carbon electrode acts as a filler material that is manually added to the weld joint.
Carbon Arc Welding is used in a variety of applications, such as welding of steel structures, pipes, and sheet metal. However, it is not commonly used today due to the development of other more efficient and reliable welding processes.
9. Stud Welding
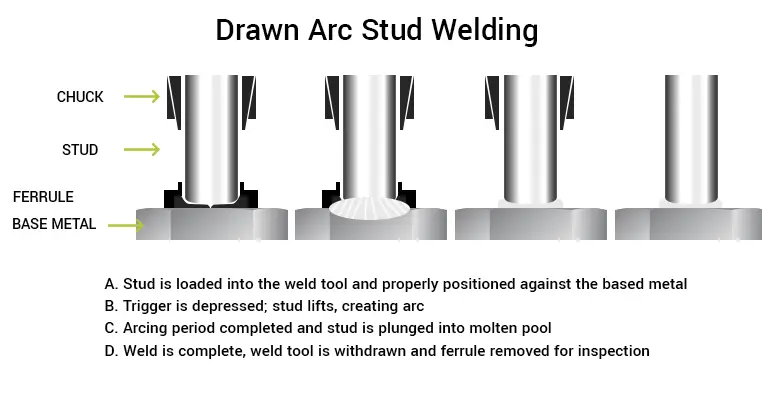
Stud welding is a welding process that is used to attach a metal stud or similar fastener to a metal base material. It is a high-speed welding process that can be used to join a wide range of metal studs and fasteners to various types of metal, including steel, stainless steel, aluminum, and brass.
In stud welding, a stud or fastener is inserted into a welding gun or hand-held tool, which holds the stud in place against the metal base material. An arc is then generated between the stud and the base material, which melts the end of the stud and the base material, forming a molten pool. The stud is then plunged into the molten pool, and the molten metal solidifies, fusing the stud to the base material.
Resistance Welding
Resistance welding is a welding process that uses an electric current to generate heat and join two metal surfaces together. In this process, two metal surfaces are held together under pressure and an electric current is passed through them, creating heat that melts the metal and fuses the two surfaces together. The current is then stopped, and the metal solidifies, creating a strong, permanent bond.
There are several types of resistance welding, including:
1. Resistance Spot Welding
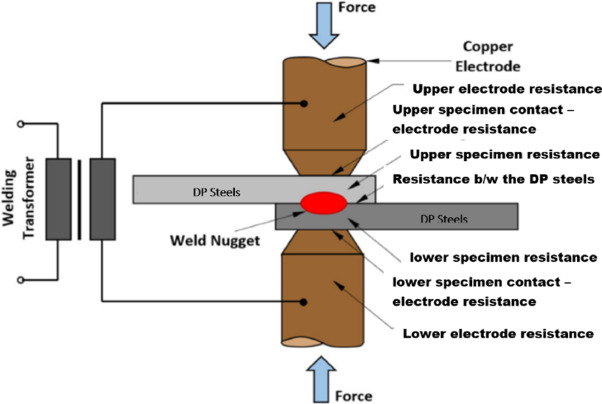
RSW stands for “Resistance Spot Welding,” which is a type of resistance welding process used to join two or more metal sheets together at discrete points. In RSW, a pair of electrodes is used to clamp the sheets together under pressure, and an electric current is passed through the sheets at the point where the electrodes meet the surface of the sheets.
The electric current passing through the sheets generates heat, which melts and fuses the metal sheets together. The heat is generated through the resistance that the metal offers to the flow of electric current, hence the name “Resistance” welding.
RSW is commonly used in the automotive and aerospace industries for joining sheet metal parts, as it produces strong, consistent welds with minimal deformation or distortion of the metal sheets. Spot welds can be made at regular intervals, and
2. RESISTANCE SEAM WELDING (RSEW)
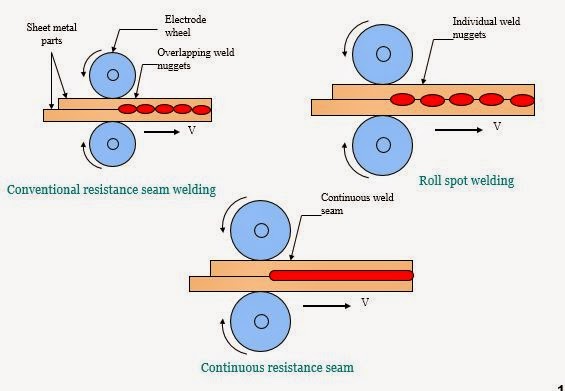
Resistance Seam Welding (RSEW) is a type of resistance welding process used to join two or more metal sheets together along a continuous seam. In RSEW, the sheets are overlapped and clamped together between two rotating electrode wheels that apply pressure and pass a high electric current through the sheets.
The electric current passing through the sheets generates heat, which melts and fuses the metal sheets together along the seam. The heat is generated through the resistance that the metal offers to the flow of electric current, hence the name “Resistance” welding.
RSEW is commonly used in the production of metal pipes, tanks, and containers, as it produces strong, consistent welds along the length of the seam with minimal deformation or distortion of the metal sheets. The seam welds are typically made with a continuous, overlapping pattern that ensures a watertight or airtight seal.
3. Resistance Projection Welding (RPW)
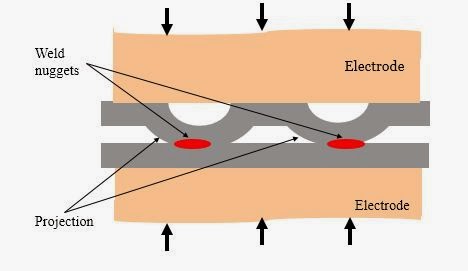
Resistance Projection Welding (RPW) is a type of resistance welding process used to join two or more metal parts with small, round projections or protrusions. In RPW, a pair of electrodes is used to clamp the metal parts together under pressure, and an electric current is passed through the projections.
The electric current passing through the projections generates heat, which melts and fuses the metal parts together at the point of contact. The heat is generated through the resistance that the metal offers to the flow of electric current, hence the name “Resistance” welding.
RPW is commonly used in the production of small metal parts, such as automotive components, electrical contacts, and fasteners, as it produces strong, consistent welds with minimal deformation or distortion of the metal parts. The projections provide a concentrated point of contact for the electric current, ensuring that the heat is generated precisely where it is needed to melt and fuse the metal.
4. Flash Welding
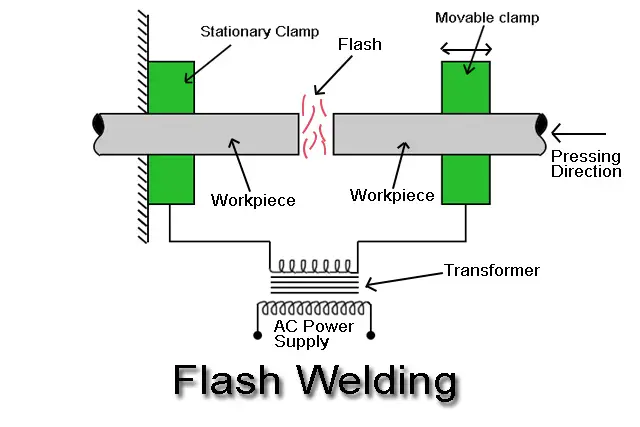
Flash Welding is a type of resistance welding process used to join two metal parts together through the application of high heat and pressure. In Flash Welding, the two metal parts are clamped together between two electrodes, and a high electric current is passed through them for a very short period of time, typically measured in milliseconds.
The electric current generates heat, causing the metal at the contact point between the two parts to melt and form a pool of molten metal. The pressure applied by the electrodes then forces the molten metal together, creating a solid weld joint as it cools and solidifies.
Flash Welding is commonly used in the production of a wide range of metal components, including rods, bars, and wires, as well as other shapes such as pipes, tubes, and fittings. It is often used in the automotive, aerospace, and construction industries, where strong, reliable welds are required.
Oxyfuel Gas Welding (OFW)
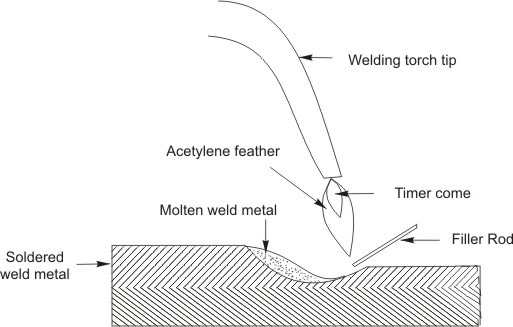
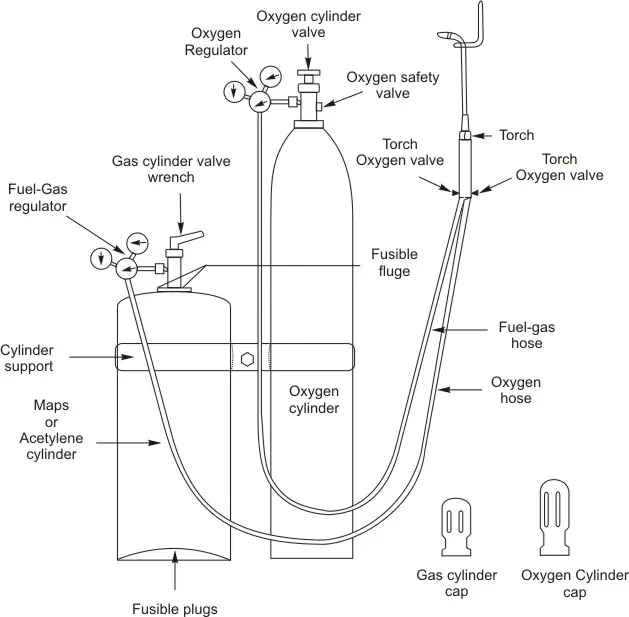
Oxyfuel Gas Welding (OFW) is a welding process that uses a mixture of fuel gases and oxygen to create a high-temperature flame that melts the metal parts being joined. OFW is commonly used in the repair and maintenance of metal parts, as well as in the fabrication of smaller metal components.
In OFW, a torch is used to mix a fuel gas, such as acetylene, with oxygen in the correct proportions to create a flame with a temperature of up to 6,300 degrees Fahrenheit. The flame is then directed onto the metal parts being joined, melting the edges of the parts and allowing them to fuse together as they cool and solidify.
OFW is a versatile welding process that can be used on a wide range of metals, including steel, stainless steel, aluminum, and brass. It is commonly used in the automotive, plumbing, and construction industries, as well as in metal art and sculpture.
Miscellaneous Fusion Welding
Laser Beam Welding (LBW)
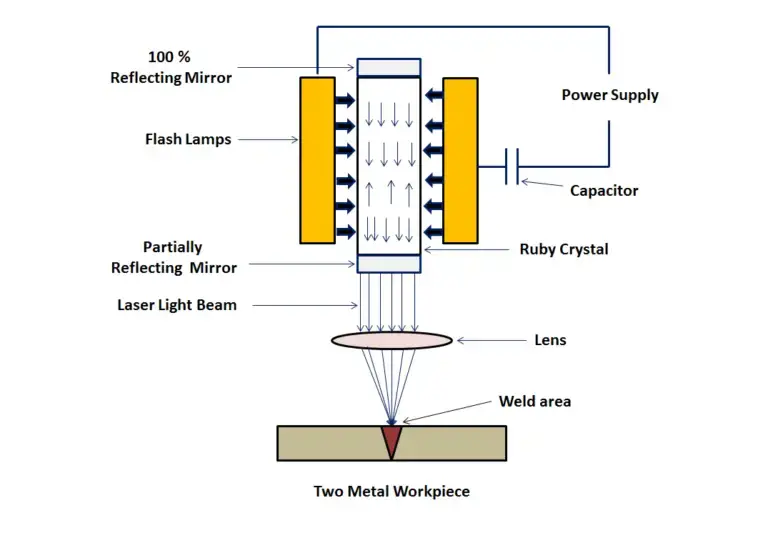
Laser beam welding (LBW) is a welding process that uses a high-energy laser beam to melt and join two metal parts together. The laser beam is typically focused onto the workpiece using a lens, and the high heat from the laser causes the metal to melt and fuse together.
LBW is commonly used in the automotive, aerospace, and electronics industries, as well as in medical device manufacturing and other precision industries. It is particularly useful for welding thin materials, such as those used in microelectronics and medical devices, due to its precise control and low heat input.
Electron Beam Welding (EBW)
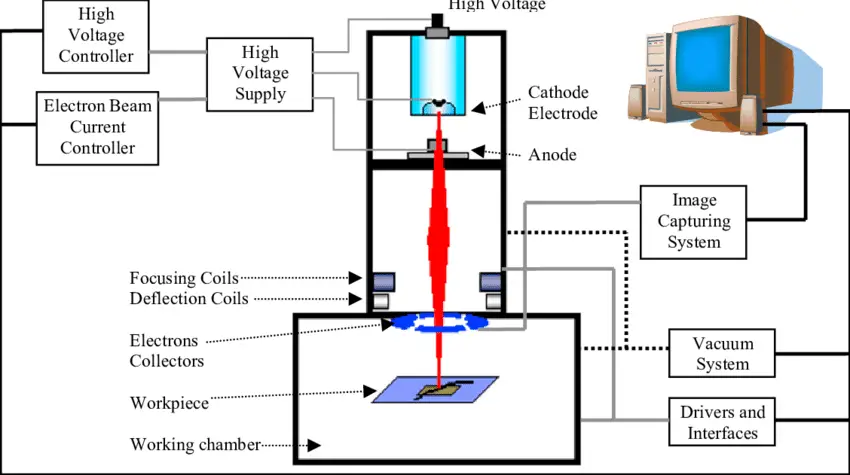
Electron beam welding (EBW) is a welding process that uses a beam of high-velocity electrons to melt and join two metal parts together. The electrons are accelerated by a high-voltage electron gun and focused onto the workpiece using electromagnetic lenses, creating a very high-energy beam that can melt and fuse the metal.
EBW is commonly used in aerospace, automotive, and semiconductor manufacturing, as well as in medical device and high-tech industries. It is particularly useful for welding small and thin parts that require high precision and minimal distortion.
Hyperbaric welding
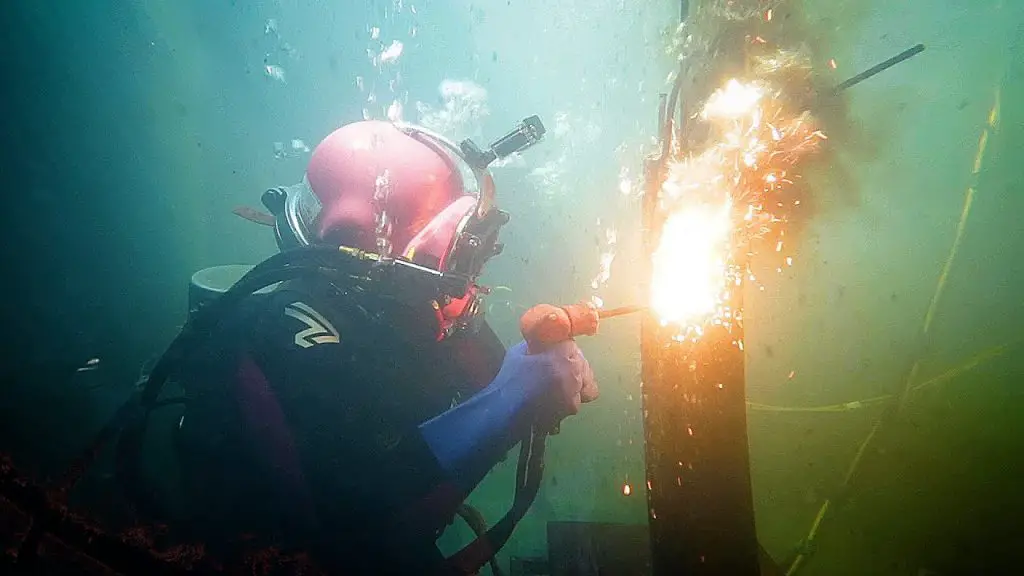
Hyperbaric welding is a technique that has gained popularity in recent years due to its unique ability to weld in underwater environments. According to a report by MarketsandMarkets, the global hyperbaric welding market size is expected to reach $338.8 million by 2025, growing at a CAGR of 3.4% from 2020 to 2025. The report cites the increasing demand for underwater repair and maintenance of offshore oil and gas pipelines and the rising adoption of hyperbaric welding in the shipbuilding and repair industry as key factors driving the market growth.
Furthermore, a study published in the Journal of Occupational and Environmental Hygiene revealed that hyperbaric welding is a safe and effective welding method in terms of worker safety. The study analyzed data from 34 commercial diving accidents and found that none of the accidents were caused by hyperbaric welding. The study concluded that hyperbaric welding is a low-risk activity when proper safety procedures are followed.
In summary, hyperbaric welding is a specialized technique that is commonly used in the construction, repair, and maintenance of underwater structures. With a growing market size and a proven safety record, hyperbaric welding is becoming an increasingly popular method for welding in challenging underwater environments.
Solid State Welding
Solid state welding is a group of welding processes that do not involve melting of the workpieces. Instead, the metal parts are joined together by applying pressure, heat, or both, and causing the atoms of the metals to diffuse across the joint, creating a solid-state bond. Solid state welding is commonly used for materials that are difficult to weld by conventional fusion welding processes or for applications where heat distortion or metallurgical changes are a concern.
Solid state welding is known for producing high-strength and high-quality welds. It is commonly used in industries such as aerospace, defense, and nuclear power, where the materials used must meet high standards of strength and durability.
Some of the common types of solid-state welding include:
Diffusion Welding (DFW)
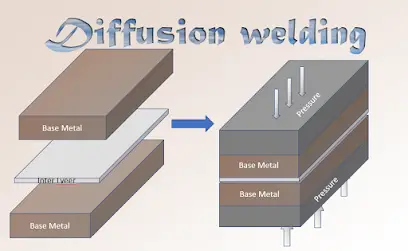
DFW stands for Diffusion Welding, which is a solid-state welding process that creates a joint between two metal parts by heating and pressing them together under high pressure, without melting the metal. The process relies on the diffusion of atoms across the interface of the two parts to create a strong, permanent bond.
In diffusion welding, the two parts to be welded are placed in contact with each other and heated to a temperature below their melting point, typically in a vacuum or an inert gas atmosphere. Pressure is then applied to the parts, causing them to deform and come into intimate contact, which allows the atoms to diffuse across the interface and bond together. The welded joint is then cooled and the pressure is released.
Diffusion welding is particularly useful for welding materials that are difficult to weld using other methods, such as high-strength alloys and refractory metals. It can also produce joints that are free of porosity and other defects commonly associated with other welding processes.
Friction Welding (FRW)
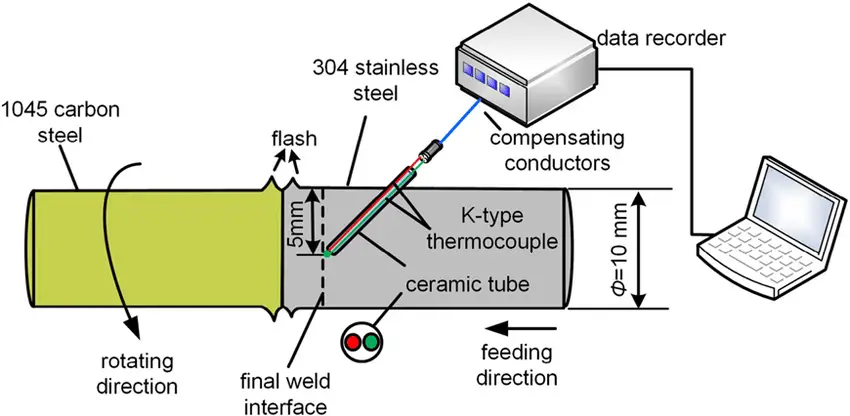
FRW stands for Friction Welding, which is a solid-state welding process that creates a joint between two metal parts by rubbing them together under pressure, generating heat that causes the metal to soften and fuse together. Friction welding can be used to join similar or dissimilar metals and can be applied to a wide range of sizes and shapes of materials.
The friction welding process involves two metal parts being brought into contact and subjected to pressure and high-speed rotational motion. This motion generates heat at the interface of the two parts, causing the metal to soften and flow together to form a solid-state bond. The welding process is complete when the rotation stops and pressure is maintained on the parts until they cool down and solidify.
Ultrasonic Welding (USW)
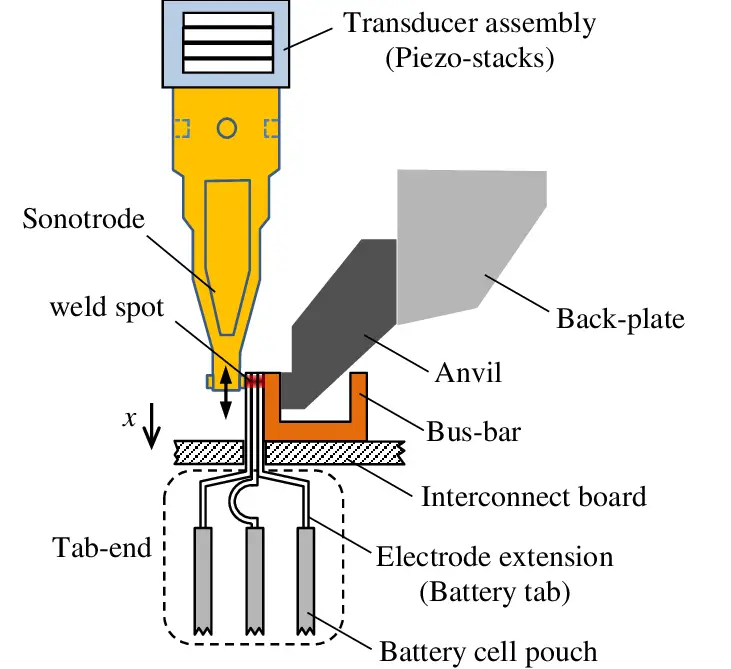
USW stands for Ultrasonic Welding, which is a solid-state welding process that creates a joint between two plastic parts by using high-frequency vibrations to generate heat and weld them together. Ultrasonic welding is commonly used in industries such as automotive, medical, and electronics, where strong and precise welds are required.
The ultrasonic welding process involves two plastic parts being placed together and subjected to high-frequency vibrations that generate heat at the interface of the two parts. The heat causes the plastic to soften and flow together, creating a solid-state bond. The welding process is complete when the vibrations stop and pressure is maintained on the parts until they cool down and solidify.
Forge Welding
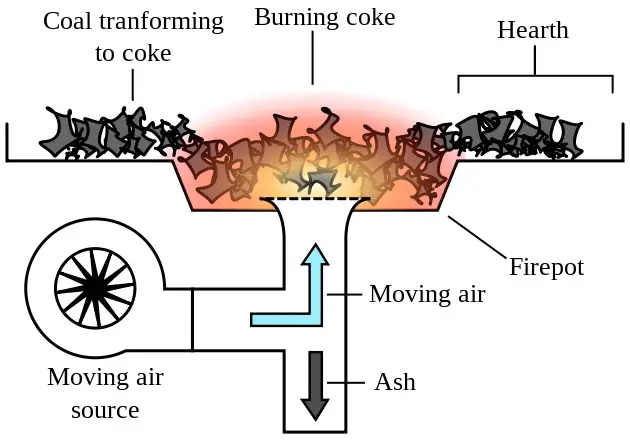
Forge welding, also known as hammer welding, is a solid-state welding process that has been used for centuries to join metals by heating them to a high temperature in a forge and then hammering them together to create a solid-state bond. It is commonly used in blacksmithing, bladesmithing, and other metalworking applications where a strong and durable bond is required.
The forge welding process involves heating two pieces of metal to a high temperature in a forge until they become soft and malleable. The pieces are then removed from the forge and placed on an anvil, where they are hammered together until they fuse into a single piece. This process is repeated several times, with the metal being heated and hammered until a strong and durable bond is created.
Cold Welding
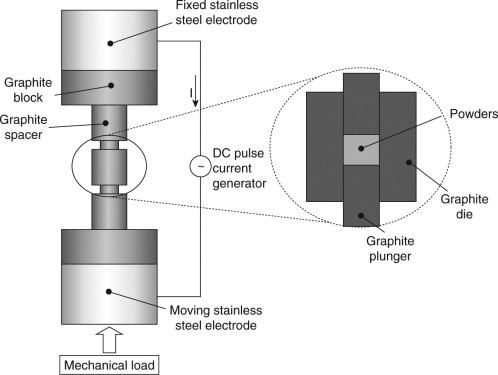
“Cold welding” is a term used to describe a solid-state welding process in which two metals are joined together without the use of heat or a filler material. This process is also known as “pressure welding” or “contact welding”. Cold welding occurs when two clean and flat metal surfaces are pressed together under high pressure, causing their atoms to diffuse and bond at the molecular level.
Cold welding is a rare and specialized process that requires highly precise conditions. The metals being joined must be extremely clean and free of any contaminants, such as oil or dust, which can prevent the atoms from bonding properly. Additionally, the surfaces being joined must be perfectly flat and free of any imperfections, as any gaps or irregularities can prevent the atoms from bonding evenly.
Roll Welding
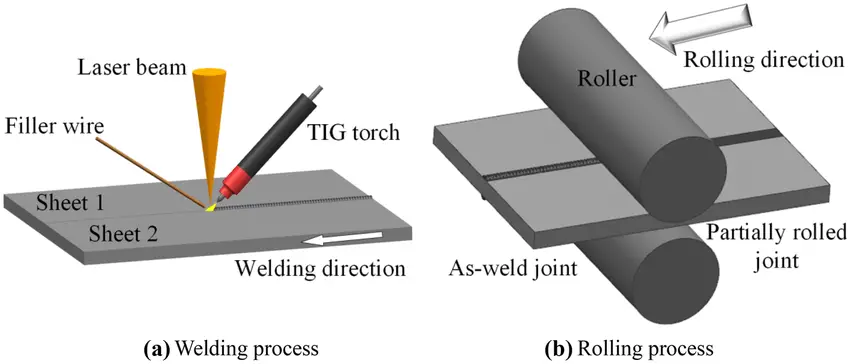
Roll welding, also known as roll bonding, is a solid-state welding process that is used to join two layers of metal by passing them through a pair of rollers at high pressure. The process is similar to cold rolling, where metal sheets or plates are passed through rollers to reduce their thickness or change their shape. In roll welding, the two layers of metal are heated to a specific temperature and then passed through the rollers, where they are compressed and bonded together.
Roll welding is a cost-effective and versatile welding process that can be used to join different types of metals with varying thicknesses. It is commonly used in the manufacturing of clad metal sheets or plates, where a layer of one metal is bonded to another for improved corrosion resistance, strength, or other properties.
Hot Pressure Welding
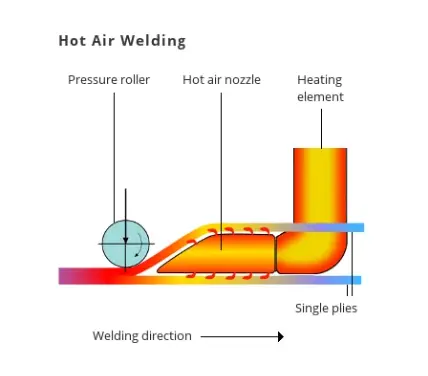
Hot pressure welding, which is also referred to as hot pressure bonding, is a welding process that creates a solid-state joint between two metal pieces by applying both heat and pressure. The process involves heating the two metal pieces to a high temperature, then applying pressure to the pieces to bond them together. The pressure is applied using a hydraulic press or other specialized equipment, which compresses the two pieces of metal and causes them to fuse together.
Hot pressure welding is commonly used in the aerospace and automotive industries for joining high-strength metals, such as titanium and nickel alloys. The process is also used in the manufacturing of electronic components, such as semiconductor devices and micro-electromechanical systems (MEMS).
Final Talk
In conclusion, welding is a crucial process that enables the fabrication of various metal structures and products. There are several types of welding processes, each with its own advantages, limitations, and applications. The choice of welding process depends on various factors such as the type of metal, thickness, and shape of materials, the required strength and durability of the weld, as well as the desired level of precision and cost-effectiveness. Welding can be used in a wide range of industries and applications, including construction, manufacturing, automotive, aerospace, and electronics. Proper training, equipment, and safety precautions are necessary to ensure successful and reliable welds. Understanding the different types of welding and their applications is essential for selecting the right welding process for a specific job and achieving strong, durable, and safe welds.