Key Notes
Here are some important things to remember about MIG welding:
Take away from the blog post
1. MIG welding, which stands for “Metal Inert Gas” welding, is a method of welding that uses a wire electrode and a protective gas to make a strong and even weld.
2. MIG welding is a quick and effective way to join metals like steel and Aluminium.
3. MIG welding makes clean welds that don’t need much cleaning up afterward. This makes it perfect for welding jobs that need a high level of precision and regularity.
4. MIG welding is easy to learn, and even newbies can do it if they have the right tools, training, and safety measures.
5. When picking MIG welding wire, you should think about the type of metal being welded, its thickness, and where you will be welding.
Overall, MIG welding is a flexible and popular way to join metals together. It can make high-quality, regular welds with little cleanup.
MIG welding, also called Gas Metal Arc Welding (GMAW), is a common way to join two pieces of metal together. It uses a continuous wire electrode. MIG welding is used a lot in industrial, automotive, and artistic settings because it can be used for many different things and works well. This website will go into detail about MIG welding, including how it works, its pros and cons, how it can be used, safety concerns, and tips for doing it well. No matter how much you know about welding or how new you are to it, this website will help you learn more about MIG welding and improve your welding skills.
How Does MIG Welding Work?

MIG welding is done with a wire electrode that is fed through a welding gun and onto the workpiece in a steady stream. The welding gun also puts out a shielding gas that keeps the atmosphere from getting into the molten weld pool.
When the operator pulls the trigger on the welding machine, the welding machine is turned on and the flow of shielding gas begins. The welding machine also sends a current through the wire electrode, which makes an arc with the workpiece. The wire electrode and the workpiece are fused together by the arc’s heat.
As the wire electrode melts, it fills the space between the two pieces of metal that are being joined. By moving the welding gun along the joint, a steady bead of weld metal is put down. The quality of the weld depends on how fast the welding gun is moved, how the gun is held, and how far away the gun is from the workpiece.
MIG welding can be done with different types of welding wire and shielding gases, depending on what the project needs. Steel, aluminium, and stainless steel are all common materials for welding wire, and argon, helium, or a mixture of the two can be used as a shielding gas.
Features of a Weld in Related MIG Welding
A weld made with MIG welding has several unique qualities, such as:
- Strong Bond: When MIG welding two pieces of metal together, the filler material and the complete fusing of the workpieces create a strong bond between the two pieces of metal.
- Strong Bond: When MIG welding two pieces of metal together, the filler material and the complete fusing of the workpieces create a strong bond between the two pieces of metal. Smooth Look: MIG welding makes a weld bead that looks smooth and clean and doesn’t need much cleaning or finishing after the weld.
- High Deposition Rate: MIG welding can be done at a high deposition rate, which means that welding can be done faster and more work can be done.
- Versatility: MIG welding can be used on a wide range of materials, such as steel, aluminium, and stainless steel, making it a versatile welding method.
- Low Spatter: MIG welding makes very little spatter, which makes the welding process faster and easier to clean up.
- Consistency: MIG welding can make welds that are the same every time. This means that even in mass production, high-quality welds can be made.
- Ease of Use: MIG welding is easy to learn and can be done with little training. This makes it a popular choice for both hobbyists and professionals.
You may like to know more about Welding Process
Features of a Weld
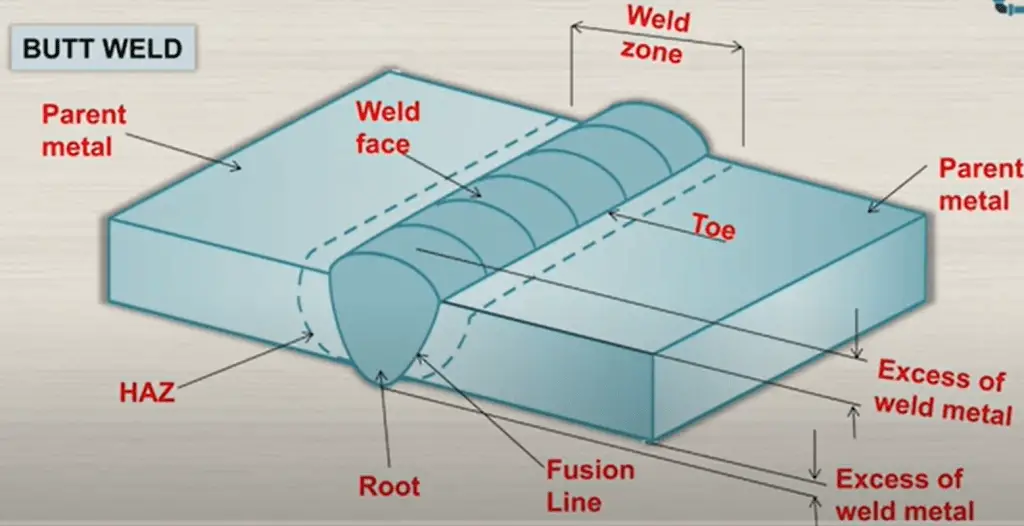
Here are some of the parts of a weld and what they mean:
- Parent Metal: The pieces of metal that are being welded together are called “parent metal.” These pieces might be made of the same thing or something else.
- Filler Metal: During the welding process, filler metal is used to join the parent metals together. The filler metal could be the same as the parent metal or it could be different.
- Weld Metal: The melted and fused material that comes out of welding is called “weld metal.” It’s where the filler metal and the base metal have joined together to make a strong bond.
- Heat Affected Zone (HAZ): The heat affected zone is the area around the weld where the temperature is high enough to change the microstructure of the parent metal. Because of the heat of the welding process, its hardness, strength, and other physical properties may change.
- Fusion Line: The line where the parent metal and the weld metal meet is called the fusion line. It is where the parent metal and the weld metal have melted together.
- Weld Zone: The weld zone is the whole area where the parent metal, filler metal, and weld metal come together to make the weld. It includes the heat-affected zone, the fusion line, and the weld metal itself.
Materials that are often used in MIG welding
MIG welding can be done on many different things, such as:
- Steel: Carbon steel, mild steel, and stainless steel are all types of steel that are often welded with MIG. In most MIG welding jobs, carbon steel is the most common material.
- Aluminum: MIG welding is also often used on aluminium, which is a light metal that is used a lot in the auto industry and in space travel.
- Copper and brass: MIG welding can also be used on copper and brass, which are both good electrical conductors and are often used in plumbing and electrical work.
- Nickel alloys: Nickel alloys, which are often used in the aerospace and power industries, can also be welded with MIG.
- Magnesium: You can also use MIG welding on magnesium, which is a light metal that is often used in aerospace.
- Titanium: MIG welding can also be used on titanium, which is a strong, lightweight metal that is often used in the aerospace and medical industries.
For a successful weld, it is important to choose the right wire and shielding gas for each type of material being welded.
Equipment and Supplies Necessary for MIG Welding
You will need the following tools and materials to do MIG welding:
- A MIG welder: is the most important piece of equipment for MIG welding. It has a power source, a wire feeder, and a gun for welding.
- Welding Gun: A welding gun is used to direct the wire electrode and shielding gas onto the workpiece.
- Wire Feeder: A wire feeder is used to move welding wire from a spool to the welding gun.
- Welding Wire: The consumable material used to make the weld is welding wire. It comes in various sizes and types depending on the material being welded.
- Shielding Gas: A shielding gas is used to keep the atmosphere from getting into the weld. Argon, helium, and carbon dioxide are some of the most common shielding gases used in MIG welding.
- Regulator and Flowmeter: A regulator and flowmeter are used to control the flow and pressure of the shielding gas.
- Ground Clamp: A ground clamp is used to connect the workpiece to the welding machine, making a complete electrical circuit.
- Welding Table or Workbench: You need a sturdy welding table or workbench to give you a stable place to work and keep things from moving around while you weld.
- Personal Protective Equipment: Welding creates bright light, heat, and sparks that can be dangerous to the welder. So, to keep from getting hurt, you need personal safety gear like a welding helmet, gloves, and safety glasses.
- Welding Accessories: You may need extra welding tools, like pliers, wire cutters, and chipping hammers, to prepare the workpiece and keep the welding equipment in good condition.
Basic Components of a MIG Welder
A MIG welder is made up of a few basic parts, such as:
- Power Source: A MIG welder’s power source changes the AC or DC power coming in to a voltage and amperage that is good for welding.
- Wire Feeder: The job of the wire feeder is to move the welding wire from the spool to the welding gun.
- Welding Gun: The tool used to make the weld is the welding gun. It has a handle, a trigger, and a nozzle. The welding wire and shielding gas are fed through the nozzle.
- Electrode Wire: The electrode wire is the wire that is used to make the weld. It is fed through the welding gun.
- Shielding Gas Supply: The shielding gas supply gives the weld the gas, like argon or carbon dioxide, that it needs to stay clean and safe from air pollution.
- Regulator: This part controls the flow and pressure of the shielding gas as it goes into the welding gun.
- Ground Cable: The ground cable is connected to the workpiece and gives the electrical current a way to complete the welding circuit.
- Control Panel: The control panel has different settings that let the welder change the welding process’s voltage, amperage, and other factors.
- Cooling System: Some MIG welders have a cooling system that keeps the machine from getting too hot during long welding sessions.
- Welding Cart: Many MIG welders are mounted on a welding cart, which lets them move around and stores extra parts and tools.
Types of Shielding Gases Used in MIG Welding
A shielding gas is necessary during MIG welding, also known as Gas Metal Arc Welding (GMAW), to protect the weld pool from contaminating the atmosphere. The type of metal being welded and the desired weld qualities will determine the best shielding gas to use. The most popular shielding gases for MIG welding are listed below:
- Argon: The most used shielding gas for MIG welding is argon. It is inert and offers enough protection for the majority of metals, including carbon steel, stainless steel, and aluminum.
- Carbon dioxide (CO2): Carbon dioxide can be used alone or in combination with argon to weld carbon steel, and it is less expensive than argon. However it causes more spatter and might result in a less appealing weld.
- Helium: Helium and argon are combined to fuse non-ferrous metals like copper, magnesium, and aluminum. It increases penetration and delivers more heat, but it also raises the possibility of porosity.
- Oxygen (O2): To boost arc stability and penetration, oxygen is utilized in modest concentrations (less than 5%) in combination with argon or CO2. Yet, an excess of oxygen can cause oxidation and porosity.
- Nitrogen (N2): To increase weld strength and decrease porosity, nitrogen is occasionally combined with argon or CO2. Duplex stainless steel is also welded using this method.
The type and thickness of the metal being welded, the desired look of the weld, and the cost of the gas all play a role in the choice of shielding gas. In order to obtain a high-quality weld, it is crucial to use the right shielding gas.
Types of Metal Cored or Flux-Cored Wires utilizes MIG Welding
A common welding method that offers high deposition rates and excellent weld quality is MIG welding with metal cored or flux-cored wires. The type of metal being welded, the welding position, and the required weld qualities all influence the wire selection. The most typical types of metal- or flux-cored wires used in MIG welding are the following:
- Carbon steel cored wire: Carbon steel and low-alloy steels are welded with carbon steel cored wire. It produces a stable, smooth arc with little spatter and high deposition rates.
- Stainless steel cored wire: Stainless steel and high-alloy steels are welded using stainless steel cored wire. It generates a clean, smooth weld with little color change and has high corrosion resistance.
- Aluminum cored wire: Aluminum and aluminum alloys are welded using aluminum cored wire. High deposition rates are offered, and a clean, smooth weld with little spatter is produced.
- Nickel cored wire: Nickel alloys like Inconel and Monel are welded using nickel cored wire. It generates a strong, ductile weld and has high corrosion resistance.
- Copper cored wire: Copper and copper alloys are welded using copper cored wire. It produces a stable, smooth arc with little spatter and high deposition rates.
- Hardfacing cored wire: This wire is used to give metal surfaces wear-resistant qualities. It is frequently used in industrial machinery, agricultural machinery, and mining equipment.
The kind and thickness of the metal being welded, the welding position, and the required weld qualities all influence the choice of flux-cored or metal-cored wire. To get a high-quality weld, the right wire selection is crucial.
MIG Welding Unit/Gun
MIG welding, which stands for “Metal Inert Gas welding” and is also called “Gas Metal Arc Welding” (GMAW), is a common way to join two pieces of metal together. It uses a wire electrode that is used up and a shielding gas. The MIG welding unit, also called a MIG welder, is the machine that gives the welding gun power and shielding gas.
The MIG welding unit is made up of a power source, a wire feeder, and a welding gun, among other things. The power source provides the electrical current that heats and melts the welding wire, and the wire feeder makes sure that the wire moves through the gun at a steady rate. Welders use a hand-held tool called a “welding gun” to guide the welding wire and keep the welding process under control.
Most of the time, the MIG welding gun has a handle, a trigger, a nozzle, and a contact tip. The gun is held by the handle, and the flow of the welding wire is controlled by pulling the trigger. The nozzle directs the shielding gas around the weld pool to protect it from contamination from the air. The contact tip is the part of the gun that touches the welding wire and carries the electrical current to make the arc.
MIG welding machines come in a wide range of sizes and styles, from small, portable machines that can be used at home to large, industrial machines that are used in factories. When choosing a MIG welder, it’s important to think about the types of materials you’ll be welding, the thickness of the metal, and the type of shielding gas you’ll be using to make sure you get the right machine for your needs.
Basic components of a MIG welder
The most important parts of a MIG welder are:
- Power Source: This is the heart of a MIG welder. It gives the welding gun the electricity it needs to work. The power source is what gives the welding wire the voltage and amperage it needs to heat up and melt.
- Wire Feeder: The wire feeder is a motorised device that moves the welding wire through the gun at a steady rate. The wire feeder makes sure that the wire goes to the welding arc at the right speed and in the same way every time.
- Welding Gun: The welder directs the welding wire and controls the welding process with the welding gun, which is a handheld tool. The gun has a trigger, nozzle, and contact tip that work together to make the arc and direct the flow of the shielding gas.
- Shielding Gas Source: When MIG welding, a shielding gas like argon or a mixture of argon and carbon dioxide is used to protect the weld from contamination from the air. Usually, the source of the shielding gas is a gas cylinder that is attached to the welding gun.
- Ground Clamp: The ground clamp is a metal clamp that is attached to the workpiece and allows the electrical current to flow through the workpiece and complete the welding circuit.
- Control Panel: The control panel has different settings and adjustments that let the welder control the welding process, such as the voltage.
What is The Actual Process of MIG Welding
MIG welding, which is also called Gas Metal Arc Welding or GMAW, is a way to join two pieces of metal together. It uses a wire electrode that is used up and a protecting gas to keep the arc from getting too hot. Here are the main steps in the process of MIG welding:
1. Get ready: Start by cleaning the metal areas that will be welded to get rid of any dirt, rust, or other things that might get in the way. You can clean the surfaces and make sure they are smooth with a wire brush or a grinder.
2. Set up the Equipment and tools. For MIG welding, you need a welding machine, a spool of wire, a welding gun, and a supply of shielding gas. Set up the machine and connect the wire and gas source to the gun.
3. Adjust the settings: Change the settings on the welding machine for the width of the metal, the diameter of the wire, and the flow rate of the gas. Depending on the type of metal being welded, these choices will be different.
4. Position the workpiece: Clamp it in place so it doesn’t move while you weld it.
5. Start welding: Hold the gun at a 10-15 degree angle to the workpiece and pull the trigger to start the arc. Move the gun along the joint, keeping the right space between the gun and the piece of work. The weld is made when the wire electrode melts and joins with the metal.
6. Continue welding: Move the gun along the joint, keeping the speed and angle constant. If the welding machine has a constant wire feed, as you weld, the wire will move forward on its own.
7. Finish welding: Pull the trigger back to stop the spark when you get to the end of the joint. Let the metal cool for a few seconds before going on to the next step.
8. Clean up: When you’re done welding, turn off the machine and take the gas and wire out. Use a wire brush to clean the weld of any slag or spatter.
MIG welding is not hard to learn, but it does take practise to get good at it. With the right method and set-up, MIG welding can be used to make strong, high-quality welds on many types of metal.
What is Metal Transfer Modes in MIG Welding
There are different ways to move the welding wire from the electrode to the workpiece when MIG welding. These ways are called “metal transfer modes.” When MIG welding, there are four main ways to move metal from one place to another.
- Short Circuiting Mode: This mode is also called “short arc” mode. In this mode, the welding wire is sometimes cut off from the workpiece, making a number of small, fast arcs. This setting is used to weld thin materials. It puts out little heat and doesn’t spatter much.
- Globular Mode: In the globular mode, the welding wire is melted and forms large droplets that fall onto the workpiece. Most of the time, this mode is used to weld thicker materials. It creates more spatter and more heat.
- Spray Mode: In spray mode, the welding wire is melted and sprayed onto the workpiece in a fine mist. This setting is used to weld thicker materials. It gives off a lot of heat and makes very little spatter.
- Pulsed Mode: In pulsed mode, the welding wire is melted in small drops and then stopped for a short time so that the weld can cool a bit before the next drip is added. This method is used to weld thin to medium materials. It makes a moderate amount of heat and very little spatter.
The type of material being fused, its thickness, and the quality of the weld you want will determine which metal transfer mode to use.
What Metals Can Be MIG-Welded?
MIG welding is a flexible method of welding that can be used to join a wide variety of metals, such as:
- Mild steel: This is the metal that MIG welding is most often used to join. It is an easy-to-weld steel with low carbon content that is used in many industrial processes.
- Stainless Steel: MIG welding is often used to join stainless steel, which is a metal that doesn’t rust and is used in many industries, such as the food industry, the pharmaceutical industry, and the aircraft industry.
- Aluminum: MIG welding can also be used to join aluminium together. Aluminum is a light metal that is used in many ways, including transportation and building.
- Copper: MIG welding can be used to join copper, which is a good conductor of electricity and is used in electrical uses.
- Nickel metals: You can use MIG welding to join different nickel metals, which are known for being strong and resistant to corrosion.
- Titanium: MIG welding can also be used to join titanium, which is a strong but lightweight metal used in many fields, such as aircraft and medicine.
The type of metal being welded and the desired qualities of the weld will determine which welding wire and shielding gas to use.
What are the Applications of MIG Welding
MIG welding is a common and useful way to join metals together. It can be used for many different things. Some of the most popular ways MIG welding is used are:
- Manufacturing: MIG welding is used a lot in the manufacturing industry to join metal parts and pieces for cars, tools, and industrial equipment, among other things.
- Construction: In the building industry, MIG welding is used to join structural steel, pipes, and other metal parts.
- Repair and Maintenance: MIG welding is used to fix and maintain machines, tools, and cars, as well as to make new parts.
- Fabrication: MIG welding is used to make metal structures, frames, and covers that are unique to each person.
- Artistic and Sculptural Welding: MIG welding can also be used for artistic and sculptural welding. This lets artists and designers make detailed metal sculptures and works of art.
- DIY Projects: MIG welding is often used for do-it-yourself projects like making metal furniture, fixing metal things, or making custom metal art.
Overall, MIG welding is a flexible and widely used method of welding that is important in many fields and uses.
What are Advantages of MIG Welding
MIG welding has a number of benefits over other ways to weld, such as:
- Versatility: MIG welding can be used to join a wide range of metals, including steel, aluminum, copper, and nickel alloys. This makes it a flexible way to join metals.
- Efficiency: MIG welding is a relatively fast welding method that can make high-quality welds quickly and efficiently, saving time and increasing efficiency.
- Ease of use: MIG welding is easy to learn and use, so both skilled welders and people who like to do things on their own often choose it.
- Quality of the weld: MIG welding makes high-quality welds that are strong, flexible, and look good. This makes it useful for a wide range of uses.
- Low spatter: MIG welding makes very little spatter, which cuts down on cleaning time and makes the metal look better overall.
- Continuous welding: MIG welding can be used for continuous welding, which is great for joining long pieces of metal without stopping.
- Precise control: MIG welding lets you control the voltage, wire feed speed, and shielding gas very precisely. This makes it possible to make welds that are uniform and can be done over and over again.
Overall, MIG welding is a flexible and effective method of welding that makes high-quality welds with little dust. This makes it a good choice for many welding jobs.
What are Limitations of MIG Welding
MIG welding has many good points, but it also has some problems, such as:
- Thickness of the material: Most of the time, MIG welding is used for smaller materials, usually up to 1/2 inch thick. Other ways of welding, like stick welding or TIG welding, may be better for stronger materials.
- Wind sensitivity: MIG welding is sensitive to wind and air movement, which can break the shielding gas and change the quality of the weld. When welding outside, wind screens or other steps may be needed to keep the environment stable.
- Access to the joint: MIG welding needs good access to the joint that is being welded, which can be hard in some cases. Other welding methods, like TIG welding, may be better for tight spots or places that are hard to get to.
- Cost of equipment: MIG welding equipment can be pricey, especially if it is high-quality and has a lot of features and options.
- Shielding gas requirements: For MIG welding, you need a source of shielding gas, which can be expensive and needs to be handled and stored carefully.
- Surface preparation: For MIG welding to work well, the surface must be clean and properly prepared. Rust, oil, and other impurities can affect the quality of the weld and may take more steps to prepare.
Overall, MIG welding is a flexible and effective way to join metals together. However, it may not be right for every welding job, and its limitations should be carefully thought through before choosing this method.
What is the difference between a MIG and TIG welding?
MIG (Metal Inert Gas) welding and TIG (Tungsten Inert Gas) welding are both common ways to weld, but they are very different in several important ways:
- Welding process: MIG welding is a semi-automatic welding method that uses a continuously fed wire electrode and a shielding gas to make a weld. TIG welding is a type of manual welding that uses a tungsten electrode and a different filler material. The filler material is fed into the weld pool separately from the tungsten electrode.
- Speed: MIG welding is usually faster than TIG welding because the wire is fed in continuously. This means that the welding process doesn’t have to stop and start as often. Because the filling material has to be added by hand, TIG welding is usually slower and takes more time.
- Quality of the weld: TIG welding makes welds that look good and are strong. This makes it a popular choice for welding important parts or in situations where the weld must meet strict quality standards. High-quality welds can also be made with MIG welding, but the quality may not be as constant as it is with TIG welding.
- Position for welding: MIG welding is easier to do in any position, including high and vertical. TIG welding is harder to do in some places, like when you’re welding from above.
- Materials: Most of the time, MIG welding is used to join steel, aluminum, and other non-ferrous metals. TIG welding, on the other hand, is usually used to join aluminum, magnesium, copper, and other unusual materials.
- Equipment: For MIG welding, you need a machine, a wire feeder, and a source of shielding gas. For TIG welding, you need a machine, a tungsten electrode, and a different filler material.
Overall, MIG welding is a fast and flexible method that works best with thicker materials. TIG welding, on the other hand, is an exact and high-quality method that works better with thin or unusual materials. Both processes have pros and cons, and which one to use will rely on the needs of the welding application.
How to Weld – MIG Welding Step by Step Guide
Step 1: Pick the right tools and supplies
Make sure you have the right tools and materials before you start MIG welding. A MIG welding machine, welding wire, shielding gas, contact tips, and a welding cap are all things you will need.
Step 2: Figure out how it works.
MIG welding tools work by feeding a reel of welding wire through a gun and into the weld joint. The electric spark melts the wire, which then sticks to the metal being joined. The shielding gas, which is often a mix of argon and carbon dioxide, keeps the atmosphere from getting into the weld.
Step 3: Put on the right safety gear.
MIG welding makes a lot of heat and light, so it’s important to wear the right safety gear, like a welding helmet with a dark mask, welding gloves, and a welding jacket or apron.
Step 4: Get your piece ready
You have to get your workpiece ready before you can start welding. This could mean cleaning the metal, getting rid of any rust or paint, and making sure the metal is in the right place to be welded.
Step 5: Put a bead down.
Hold the gun perpendicular to the workpiece and pull the trigger to start the flow of shielding gas. This will start the weld. Then, pull the trigger again to start the wire feed, and lay a bead of wire along the joint. Make sure to keep your hand steady and keep the space between the gun and the piece of work the same.
Step 6: Join the metal pieces together.
After laying a bead, continue welding the metal together, making sure to move the gun in a smooth, steady motion. Don’t stop and start, because this can lead to holes or welds that aren’t even.
Step 7: Grind the weld smooth.
After the weld is done, use a tool to smooth out any rough spots or uneven areas. This will make the weld look clean and well done.
Step 8: Fix the most common issues
MIG welding can be hard, and it’s normal for problems like porosity, spatter, and burn-through to happen. If you run into any of these problems, you might need to change the way you weld or your tools to get the best results.
Step 9: If you need to, replace or fuse the wire.
As you weld, you will need to change or fuse new welding wire onto the spool in the machine. Make sure to follow the right safety rules and don’t touch the wire or the machine while it’s going.
What Factors Need to Consider When Choosing MIG Welding Wire
There are a few things to think about when picking MIG welding wire. Here are some things to think about:
- Type of metal being joined: The type of wire to use will depend on the type of metal being joined. For example, if you are soldering mild steel, you should use a wire with a core made of mild steel.
- Width of the wire: The amperage and thickness of the metal that can be welded depend on the width of the wire. bigger wire can join bigger pieces of metal, but it needs more amperage.
- Composition of the wire: The quality of the weld can be affected by what the wire is made of. For example, some lines are made to be strong or to have little sparking.
- Shielding gas: The type of wire to use will also depend on the type of shielding gas being used. For example, if you are using a mixture of argon and carbon dioxide (CO2), you will need to use a wire that is made for that combination of gases.
- Position: How you will be welding (flat, horizontal, vertical, or overhead) will also affect which wire you choose. Some wires are made for certain situations of welding.
- Welding application: The choice of wire will also depend on how the weld will be used. For example, if the weld will be put under a lot of stress or be exposed to rust, you will want to use a wire that is made for that kind of job.
- Cost: Cost is the last thing to think about when picking welding wire. Some lines cost more than others, but they might work better or last longer if they do.
By thinking about these things and picking the right wire for your welding project, you can make sure you get good welds and finish your welding project successfully.
FAQ
Is MIG welding hard to learn?
MIG welding, which is also called Gas Metal Arc Welding or GMAW, is thought to be one of the easier ways to learn how to weld, especially when compared to TIG welding or Stick welding.
For MIG welding, you run a wire through a welding gun. The wire melts and fuses with the base metal, making a strong bond. It also has a fairly high deposition rate and can be used to join a wide range of metals and sizes.
But, like any other skill, MIG welding takes time to learn. To get good at welding and make regular, high-quality welds, you do need to practise. MIG welding works best when the tools are set up correctly and safety measures are taken.
With the right training, practice, and safety steps, MIG welding can be easy for DIYers, hobbyists, and professionals alike to learn and master.
Can I teach myself to MIG weld at home?
Yes, you can learn to MIG weld at home, but it’s important to take the right safety measures and practise good welding methods to avoid getting hurt and make good welds.
Here are some things you can do at home to learn MIG welding:
- Research: Start by reading up on MIG welding methods, safety precautions, and how to set up the equipment. You can learn more about the process by watching online lessons and reading books or articles about it.
- Obtain equipment: Buy or rent a MIG welding machine, a welding gun, welding wire, and protective gas. Make sure that the tools you choose are right for the type and amount of the metal you will be welding.
- Set up the equipment: Set up the welding machine and connect the gun to the wire and gas supply according to the manufacturer’s directions.
- Practice safety: Wear the right safety gear, like a welding hat, gloves, and protective clothing, at all times. Make sure your desk has good air flow and nothing that can catch fire.
- Practice welding technique: Practice your welding skills. To improve your welding skills, start by practising on scrap metal. Focus on keeping the length and speed of the arc the same, and make sure the wire is fed into the joint correctly.
- Evaluate results: Look at your welds and see where you can make them better. Use a grinder or wire brush to get rid of any slag or powder, and look for cracks, holes, or other problems in the weld.
- Keep on learning: As you gain more experience, continue to learn and improve your technique. You can learn more about welding by going to classes, workshops, or online training.
Don’t forget that welding can be dangerous, so it’s important to take the right safety measures and use good skill to avoid getting hurt and make good welds.
Do I need a welding certificate from a program or school?
Whether or not you need a certificate from a programme or school to weld depends on what you want to weld and what your employer, business, or local laws require. Here are some times when you might need a welding certificate:
Many companies want welders to have a certificate or degree from a recognised welding programme or school to show that they are skilled and know what they are doing.
Certification: Some welding jobs may require certification from a well-known welding group, like the American Welding Society (AWS). To get this certification, you usually have to pass a welding test and meet other requirements.
Regulatory requirements: Some industries or local laws may require welders to have a welding certificate or licence to make sure they are qualified to do welding jobs safely and effectively.
But if you only want to use welding for personal projects or as a hobby, you might not need a licence. In this case, you can still learn how to weld through self-study, online tutorials, or classes, and you can practise safe welding methods to make sure your welds are of good quality.
In short, whether or not you need a welding certificate relies on how you plan to use welding and what your employer, industry, or local laws require.
What type of welding is the strongest?
There is no one “strongest” type of welding because different materials and tasks call for different types of welding. But here are some types of welding that are often used because of how strong they are:
- TIG welding, also called “Gas Tungsten Arc Welding” or “GTAW,” makes strong welds that look good and are of high quality. It is usually used to weld stainless steel, aluminum, and other metals that don’t contain iron.
- Stick welding, also called “Shielded Metal Arc Welding” (SMAW), is a versatile and effective way to join metals together. It can be used to join steel, stainless steel, and cast iron. It makes strong, long-lasting welds that can stand up to a lot of stress and pressure.
- Gas Metal Arc Welding, or GMAW, is another name for MIG welding. It is a quick and easy way to make strong, even welds. It is often used to join steel and aluminium together.
- Flux-cored arc welding, or FCAW, is a type of MIG welding that uses an electrode wire with a flux core instead of a solid wire. It makes strong, well-penetrated welds and is often used to weld thick materials or outside or in windy situations.
In general, the strength of a weld relies on many things, such as the welding technique, the type of material being welded, the welding conditions, and the skill of the welder. The strength of a weld can also be affected by things like how well the weld was prepared, how clean the joint was, and what kind of filling metal was used.
MIG vs TIG vs Stick, which is best?
There is no single “best” way to weld because each method has its own pros and cons that rely on the application and the materials being welded. Here are some key differences between MIG, TIG, and Stick welding that may help you decide which method is best for your needs:
MIG welding: MIG (Metal Inert Gas) welding is a method that uses a wire electrode and a shielding gas to make a strong and consistent weld. It is a quick and effective way to join different metals together, such as steel, stainless steel, and aluminium. MIG welding is also easy to learn, makes clean welds, and requires little cleanup.
TIG welding: TIG (Tungsten Inert Gas) welding is a method that uses a tungsten electrode and a shielding gas to make a precise and high-quality weld. It is often used to weld thin metals like aluminium and stainless steel, and the weld it makes is usually clean and nice to look at. TIG welding is more difficult and takes more skill and practise to get good at than MIG welding.
Stick welding: Stick welding, also called Shielded Metal Arc Welding or SMAW, is a method that uses a stick-shaped electrode and a flux coating to make a strong and long-lasting weld. It is a trustworthy method that can be used to join different kinds of metals, like steel, cast iron, and stainless steel. Stick welding is also easy and doesn’t require much in the way of tools, so it’s great for jobs that need to be done outside or in a remote area.
In short, MIG welding is a fast and effective method that works best with thicker metals, while TIG welding is an exact and high-quality method that works best with thin and fragile metals. Stick welding is a versatile and reliable method that works best for welding jobs that take place outside or in remote places. In the end, your goals, materials, and skill level will determine which welding method is best for you.
Final Talk
MIG welding is a common and flexible method of welding that uses a wire electrode and a protective gas to make a strong, even weld. It is a quick and easy process that makes clean welds with little clean-up. This makes it perfect for welding jobs that need accuracy and regularity. MIG welding is easy to learn, and even newbies can do it if they have the right tools, training, and safety measures. When picking MIG welding wire, it’s important to think about things like the type and thickness of the metal being welded as well as the welding position. MIG welding is still a popular choice among both professional welders and people who like to do things on their own.